環境サステナビリティ
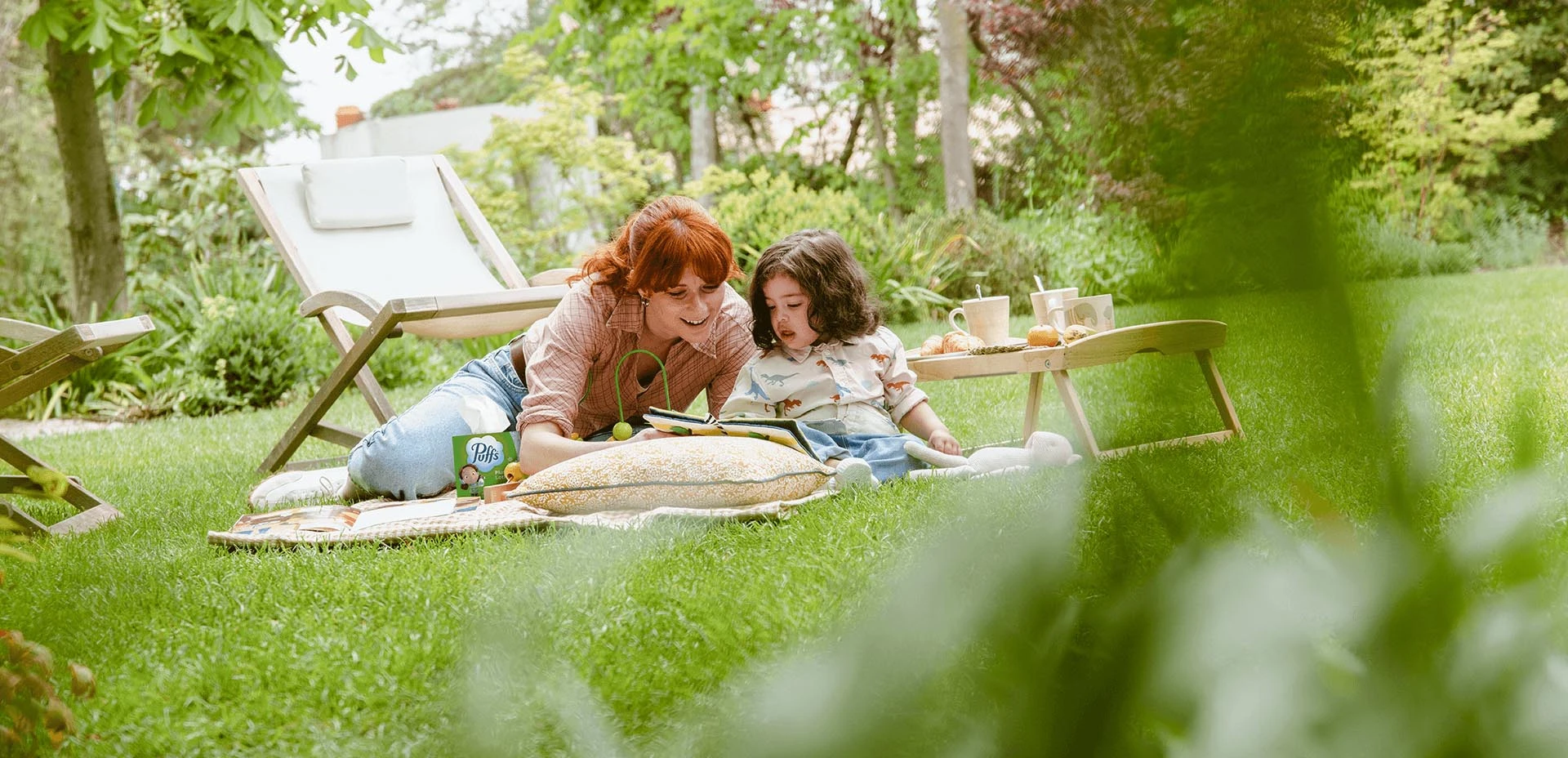
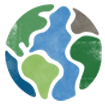
P&Gでは、環境サステナビリティを経営戦略の一環として捉えています。私たちには、社会をより良くする責任があります。「より良くする」という目標は不変ですが、その基準は時代に応じて変わっていきます。
今の時代には、消費者にとってより良い物であると同時に、地球にとってもより良いものを提供することが求められています。私達はこの考えを製品を通じて、社会と共有しています。
現代におけるイノベーションとは、圧倒的な優位性と同時に持続可能なものでなければなりません。共に動くことで、私たちはより良い未来を築くことができます。地球は私たちの故郷です。今こそ私たちが手を取り合って動く時なのです。
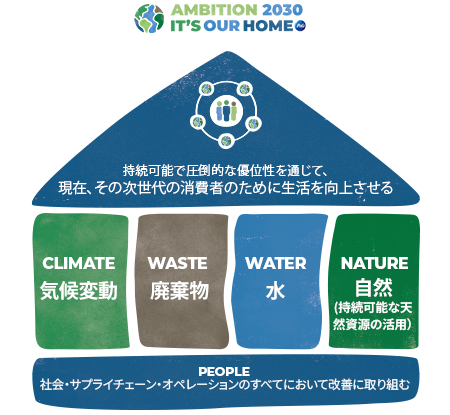
クリックすると各セクションへジャンプします。
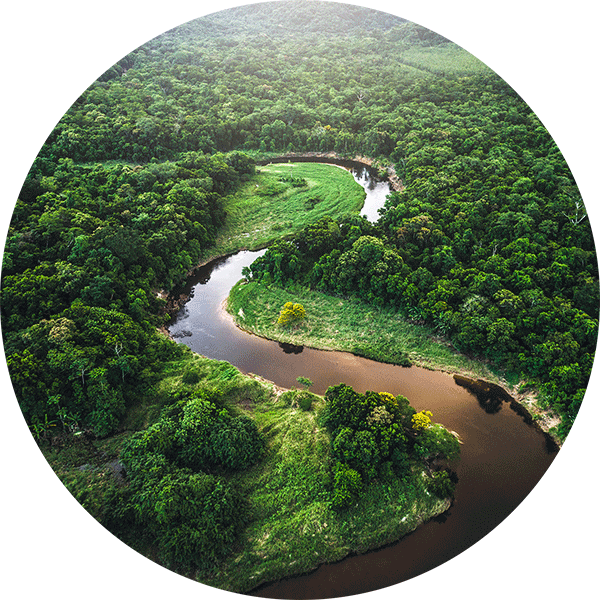
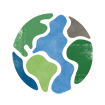
気候
2040年までに温室効果ガス排出量をNET ZERO(ネットゼロ)に
2021年9月に、P&Gは原材料の調達から自社のオペレーション・サプライチェーンまでで排出される温室効果ガスを実質ゼロにするという新たな野心的目標を設定しました。
また、P&Gは、気候変動に関する主要課題への対応を加速的に進めるための包括的な取り組みを、気候変動対策アクションプランとして発表しました。
Net Zero 2040と気候変動対策アクションプランを通じて、製品設計、サプライチェーン、工場でのオペレーションから消費者による製品の使用そして廃棄まで、いわゆる製品のライフサイクル全体を網羅します。
気候変動に関する進捗状況の詳細はこちら(英語).
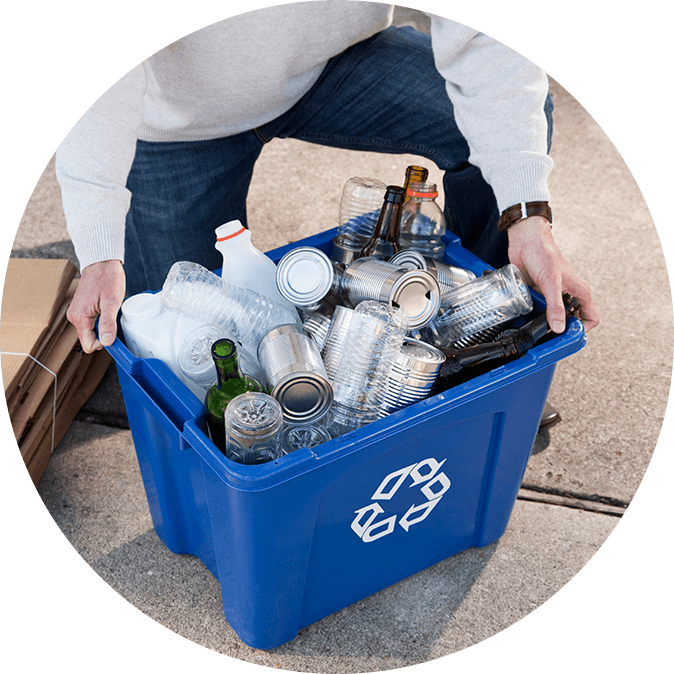
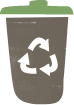
廃棄物
私たちの暮らしの中で特にプラスチック廃棄物が河川や海洋に流れ込み深刻な問題になっています。これは、プラスチックのライフサイクル全体にわたって包括的かつ協力的な対策を必要とする、複雑かつグローバルな課題です。この課題に取り組み、プラスチックの循環性をさらに高めるためには、産業界、政府、市民社会、学界を含む、様々な関係者が協力することが必要です。プラスチックは、包装材の削減、製品の保護、輸送に伴う温室効果ガス排出の削減を実現しますが、私たちは責任をもって使用し、再利用しなければなりません。
P&Gでは、2030年までに全ての消費者向けパッケージがリサイクルまたは再利用可能になるように代替素材の使用、外部連携を通じた廃棄物インフラの整備や、新しいリサイクルソリューションの開発などと通じて、プラスチックを再利用し、自然界に残さないための取り組みを進めています。
廃棄物の目標に関する進捗状況の詳細は、こちらをご覧ください(英語)
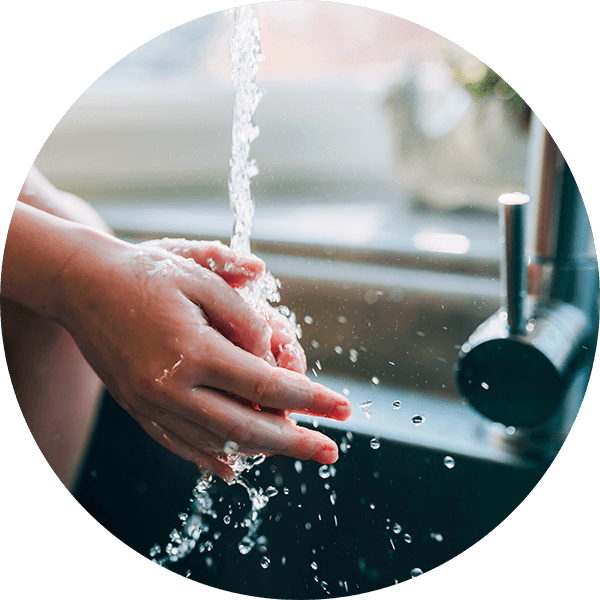
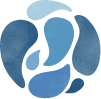
水
P&Gでは、現在そして未来の世代にわたって、人々の生活と自然を支える事の出来るウォーターポジティブな未来につながる取り組みを行います。2022年6月、私たちは、水不足地域の人や自然のために事業活動における水の使用量の削減、イノベーションとパートナーシップを通して、水資源を確保するための包括的戦略を発表しました。また、2030年の目標として、世界中18の水不足地域にあるP&Gの製造拠点で消費される水量を上回る水を還元すること[1]、ロサンゼルスやニューメキシコシティのような水不足の深刻な都市部において、P&G製品の使用により消費量よりも多くの水を還元すること[2]を掲げています。私たちはこれらの目標を、水資源を改善、管理、保護するパートナーシップと還元するためのプロジェクトを通して実現させます。
水の目標に関する進捗状況の詳細は、こちらをご覧ください。
1.これらのサイトでP&G製品の製造中に蒸発したり、最終製品に取り込まれる水。
2.家庭からの水漏れやP&G製品使用中における蒸発による水。
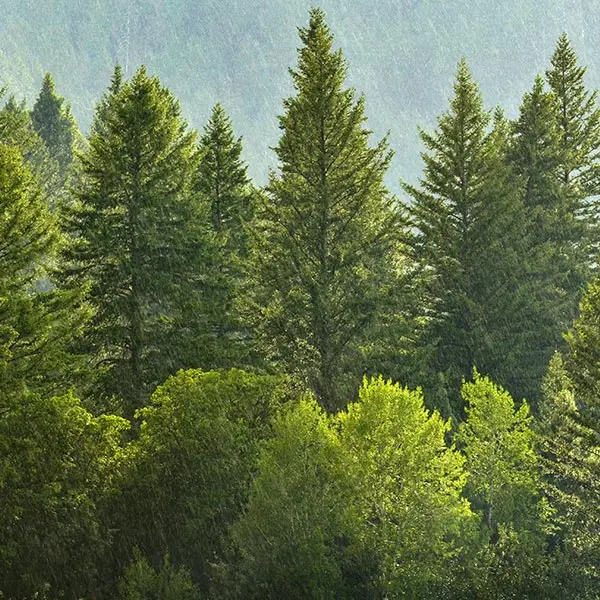
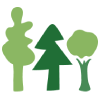
自然
P&Gでは、私たちは、人々や生物多様性と私たちの事業にとって不可欠な自然生態系が長期的に健全な状態を保つ為の取り組みを行っています。私たちの取り組みは、木材パルプ、パーム油、紙製パッケージなどの主要な商品について、責任ある調達を確保することから始まります。
また、生態系保護、改善、回復が必要な場合には、直接的なサプライチェーンだけでなくその先まで対応を広げます。私たちは、この10年間で我々のオペレーションで排出される二酸化炭素などの温室効果ガスの排出量を相殺し、
150万エーカー以上の土地にプラスの影響を与えられる投資や協働を通じて、人々と生物多様性にとって良い結果をもたらすよう取り組みを行っています。
私たちの目標に関する進捗状況の詳細は、こちらをご覧ください。
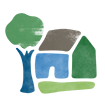
家庭でのエネルギーを節約する
2015年以降、P&Gの洗濯洗剤ブランドのタイドとアリエールの製品改良により、消費者はエネルギー消費を抑えながら洗濯が出来るようになりました。これによりおよそ1,500万トンの二酸化炭素排出削減に貢献しました。私たちは、イノベーションと、製品の使用方法に関する啓蒙、消費者への教育を通じて、二酸化炭素排出の最も大きな原因である、洗濯水の温めに必要なエネルギー削減に取り組んできました。
P&Gの取り組みはさらに続く
詳しくは、ESG投資家向けポータルページで、P&Gの目標、水、廃棄物、気候、森林、イクオリティ&インクルージョン、ガバナンスなどに関する取り組み、進捗状況をご覧ください。また、森林、パッケージ、水、気候の分野で、私たちがどのように家庭をより良くする手助けをしているか、様々なプログラムや活動に関する具体的な情報については、公式ウェブサイトのMapping Our Impactセクション(英語)をご覧ください。
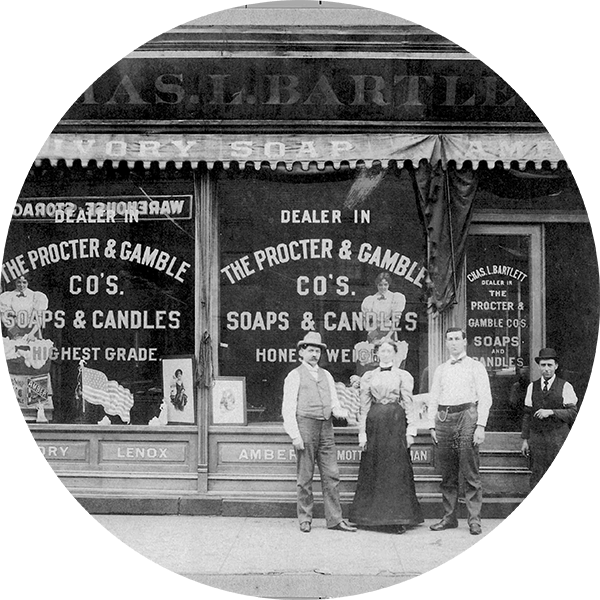
P&Gの環境サステナビリティの歴史
環境サステナビリティの取り組みの歴史はタイムラインをご覧ください。